ROTATING TANK CLEANING NOZZLE SPRAY TECHNOLOGY
Request a quote
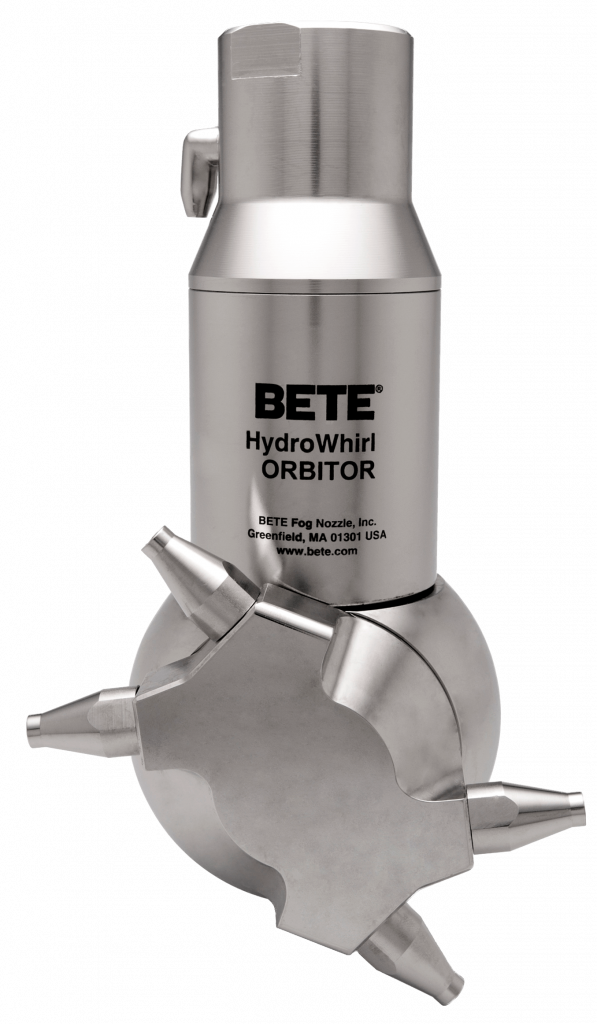
Rotary Nozzles Improve Tank Cleaning Performance Through Greater Mechanical Force, Saving You Time and Money
Tank cleaning nozzles are typically stationary or rotating, and the type of nozzle you select will depend on the requirements for your application. Static nozzles work best where clogging is a problem because they have no moving parts. Rotating tank cleaning nozzles use mechanical force to provide better spray impact for effective soil removal. Also known as rotary spray heads, these devices require less time for cleaning and use fewer resources.
We categorize BETE tank cleaning nozzles into three different operating principles. With rotary spray cleaners, mechanical force plays a vital role in cleaning efficiency and cost savings.
Equipment & Tank Cleaning Brochure
Download PDF
Tank Cleaning Spray Technology Line Card
Download PDF
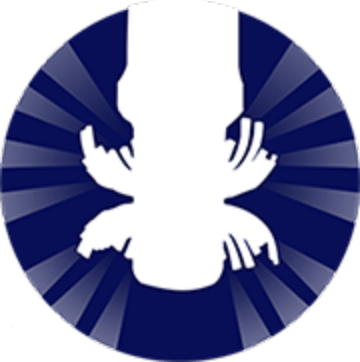
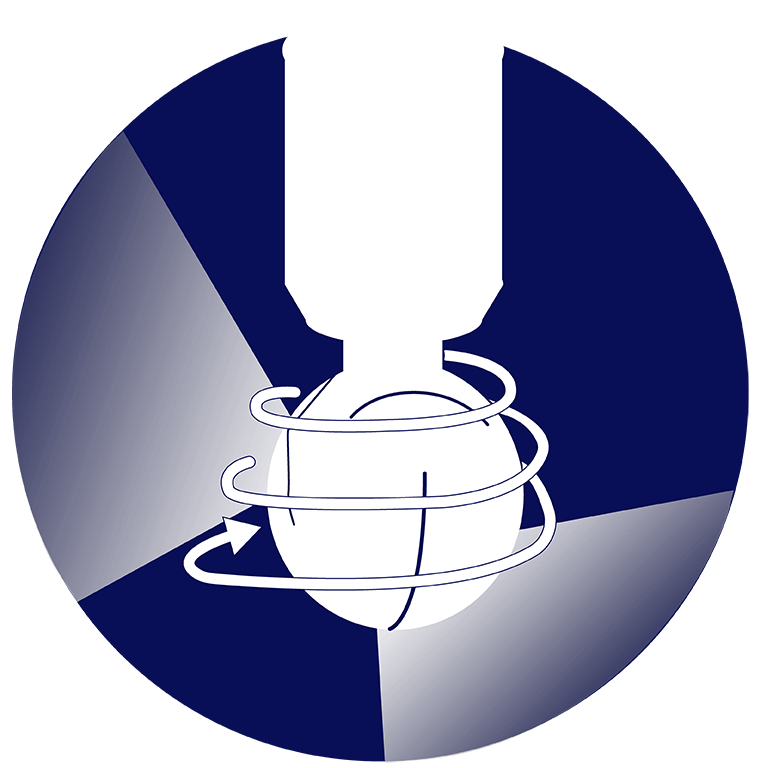
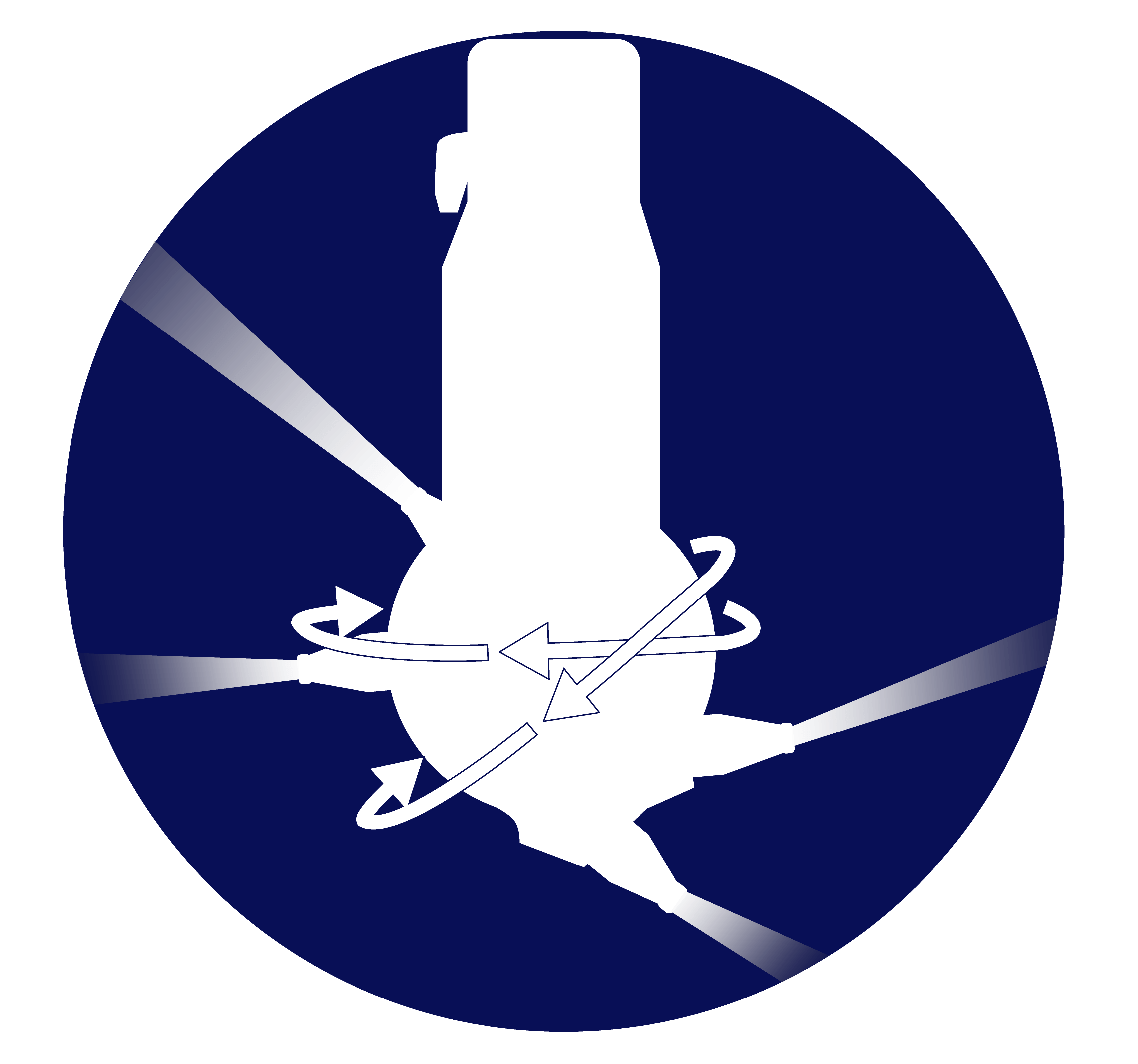
Types of Operating Principles
Please select an operating principle from the drop-down menu.
STATIONARY
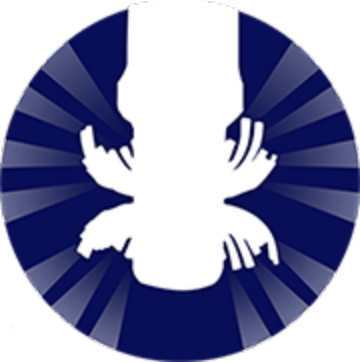
Stationary nozzles, also known as static nozzles, have no moving parts. The low-maintenance designs of our innovative HydroClaw and spiral TW provide sizable free passage superior to standard static spray balls. The versatile size range and narrow form of the TW series ensure compatibility with small vessel openings.
REACTIONARY FORCE
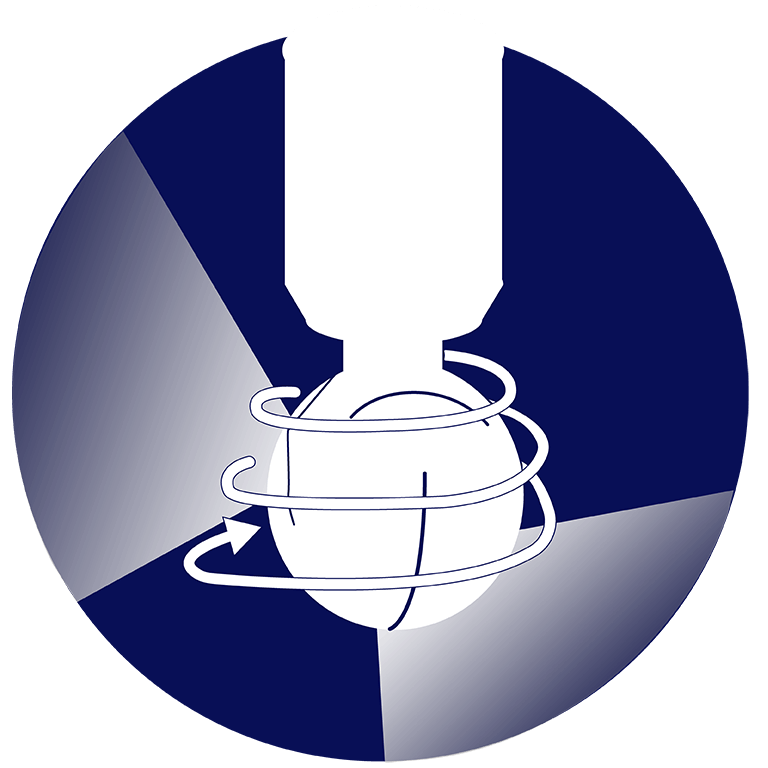
These are fluid-driven tank cleaning nozzles use the reaction force of the spray media to drive the rotation of the nozzle head. These provide complete 360° coverage and efficient cleaning through impact and repetition. Rotating nozzles increase tank washing efficiency over static spray balls, saving time and money by reducing water and cleaning agent consumption, while decreasing downtime.
ROTARY JET
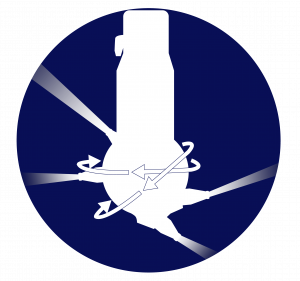
Rotary jets use the spray media flowing through internal gears on the body to rotate sets of high impact jet nozzles through an efficient 2-axis orbital pattern, providing complete 360° coverage. The jet pattern nozzles utilized on these assemblies provide significantly more impact and impingement force than other styles of tank cleaning nozzles, making them ideal for hard-to-clean residues and larger vessels.
Fundamentals of Cleaning Technology
The fundamentals of cleaning technology use the relationship between time, temperature, chemical action, and mechanical force. Mechanical force plays a vital role in this relationship and represents the spray impact applied to the surface area by the tank cleaning nozzle.
MECHANICAL FORCE
The amount of spray impact applied to the surface area by the cleaning nozzle
TIME
The duration required to clean a tank by combining mechanical force, temperature, and chemical action
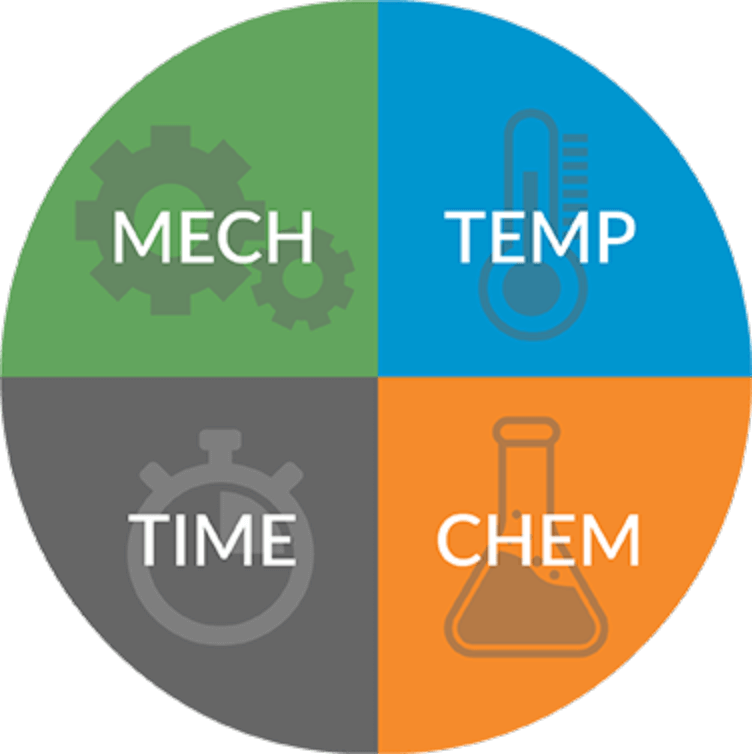
TEMPERATURE
The temperature of the cleaning cycle
CHEMICAL ACTION
Effect of chemical solutions or possibly hot water to aid in dissolving eroding soils on the tank surface
Reduce Costs With Mechanical Force
Applying greater mechanical force to the cleaning process can reduce time, temperature, and chemicals, resulting in less water consumption and effluent discharge. The illustration below compares the mechanical force of a traditional static spray ball to a rotary tank cleaning device.
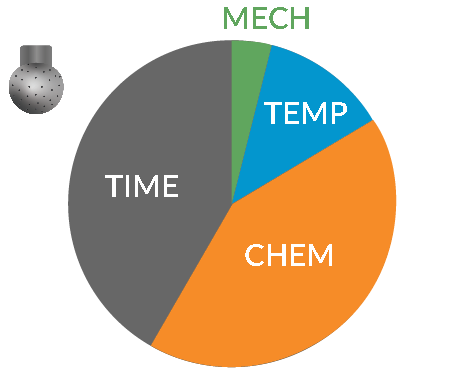
Static Spray Ball
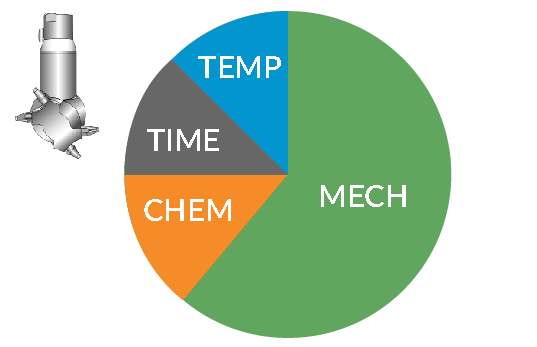
Rotary Tank Cleaning Nozzle
Static spray balls require more time to clean because they produce very little mechanical force and consume more chemicals and water, which produces extra waste and increases costs. Rotary tank cleaning nozzles provide greater mechanical force requiring less time for cleaning and benefiting from increased production and cost savings.
Need Technical Support?
For more specific information regarding your application download and complete our Tank Cleaning Application Information Request form.
Tank Cleaning Application Information Request Form
Download PDF
Related Tank Cleaning Solutions
Read Our Case Studies
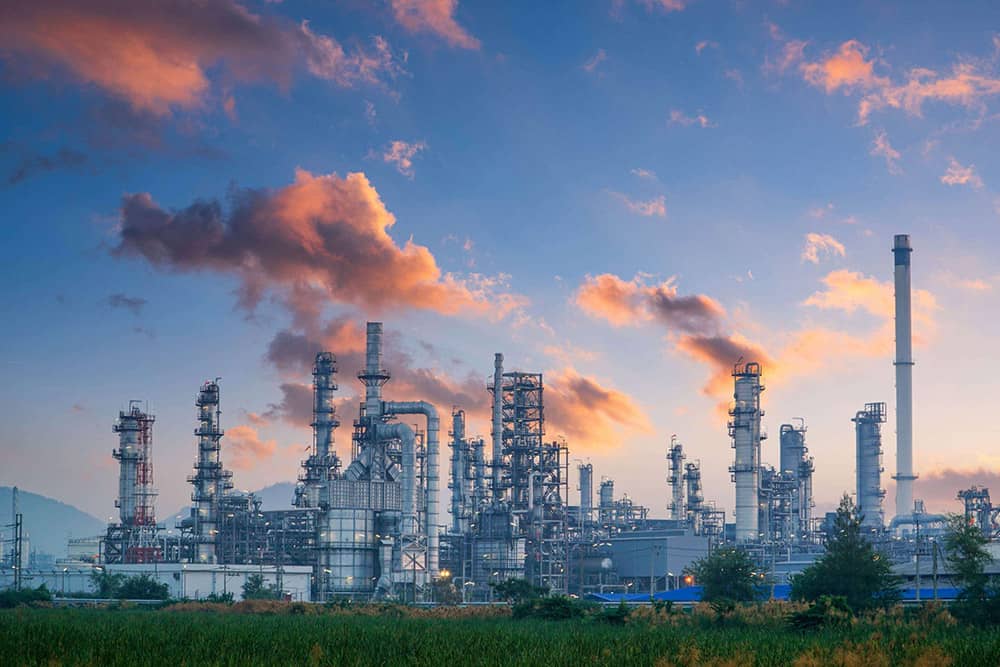
Automated Spray System for Chemical Processing Enhances Gas Cooling Performance and Reliability
A demineralized water injection system is needed to quench calciner furnace exhaust gas upstream of dust
collection equipment at a chemical processing plant during the manufacture of specialty catalyst. Spray
nozzles need to produce small droplet sizes to achieve complete evaporation, which requires pumps for
high-pressure water supply, controls, and instrumentation to regulate and monitor the gas temperature.
Read More
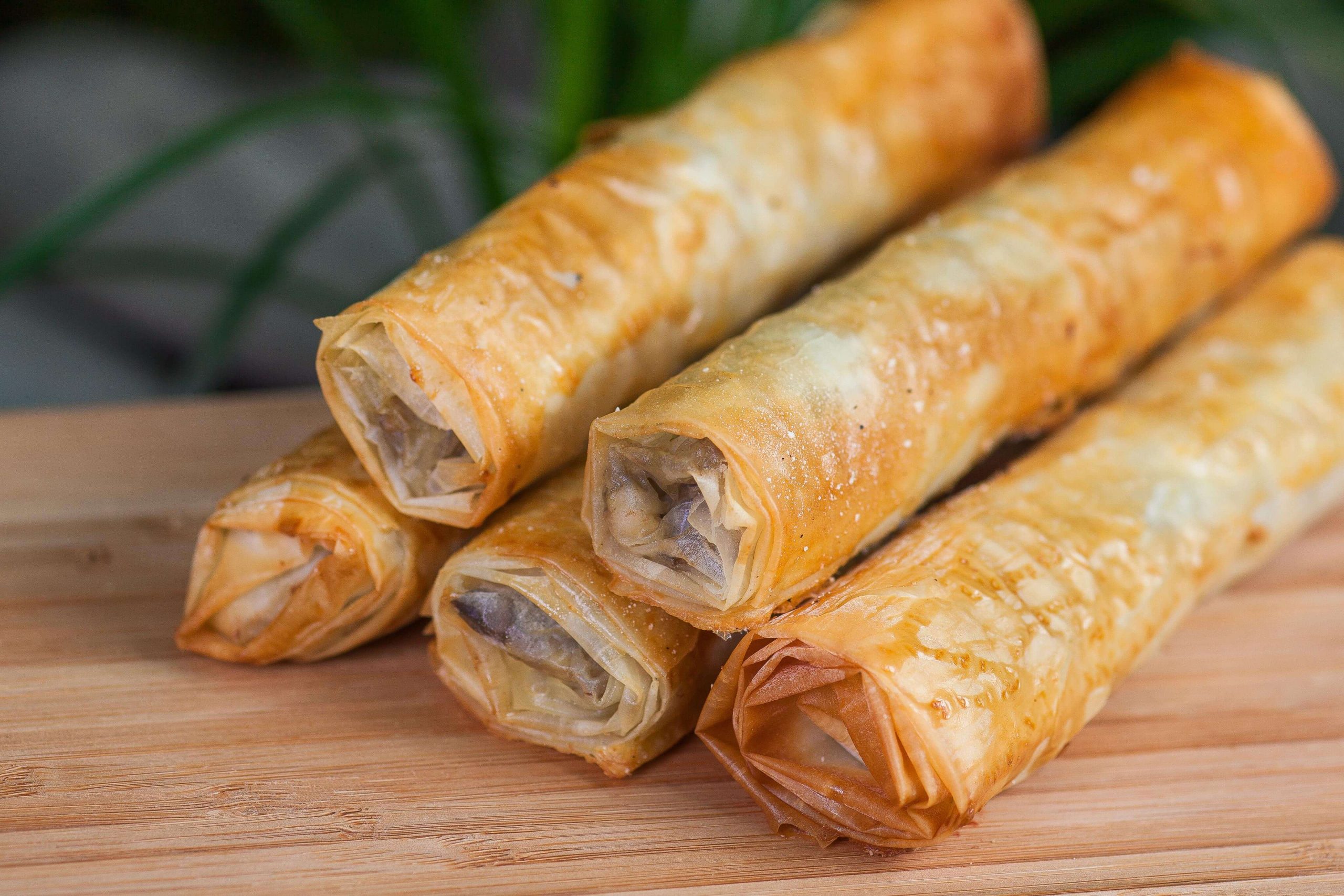
FlexFlow® Spray System Reduces Material Waste With Precision Coating for Frozen Pastry Manufacturer
Filo dough moving along an assembly line is filled with various ingredients, hand-rolled, and packaged. Before
rolling the dough, palm oil is hand-brushed by two linemen to act as the “glue” that holds the pastry together. The
manual application creates inconsistencies in the product, variation in nutritional content, excessive use of oil,
and uneven coverage – adding to the overall cost of production.
Read More
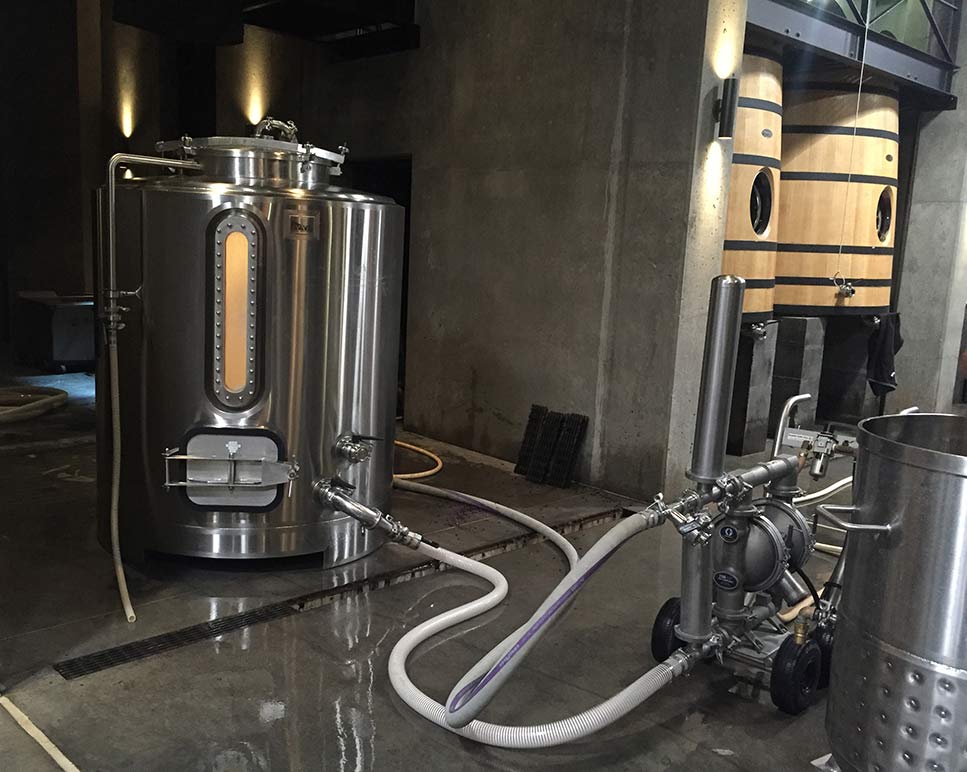
Prominent Winery Saved From Nozzle Clogging, Unwanted Maintenance, and Downtime
Even with a preliminary rinse before the cleaning process, leftover grape debris in the fermentation tanks such
as seeds, stems, and skins remain.
Read More