In packed bed scrubbers, scrubbing fluids are distributed over packing material in a column or vessel, creating a thin liquid film on the packing. As the gas to be scrubbed passes upward through the packing material, it contacts the liquid film, providing an opportunity for cooling and condensation or a chemical reaction between the scrubbing liquid and the process gas.
Packed bed scrubbers can vary widely in design and can be used in vertical or horizontal gas flow arrangements. They can be used for multiple scrubbing applications and are particularly well suited for acids, inorganic gases, soluble gases, fume control, VOCs, and odor control, among other applications.
BETE spray nozzles can evenly distribute scrubbing fluids over the packed beds to ensure even run-down through the packing and avoid any gas bypass through the scrubber. Wide coverage areas from a single point allow spray nozzles to provide simpler piping designs and greater clog resistance over pan, trough, or tray distributors. The ability of spray nozzles to provide a wide variety of spray patterns and be manufactured in almost any material allows them to be selected or custom-designed for almost any packed bed scrubber application.
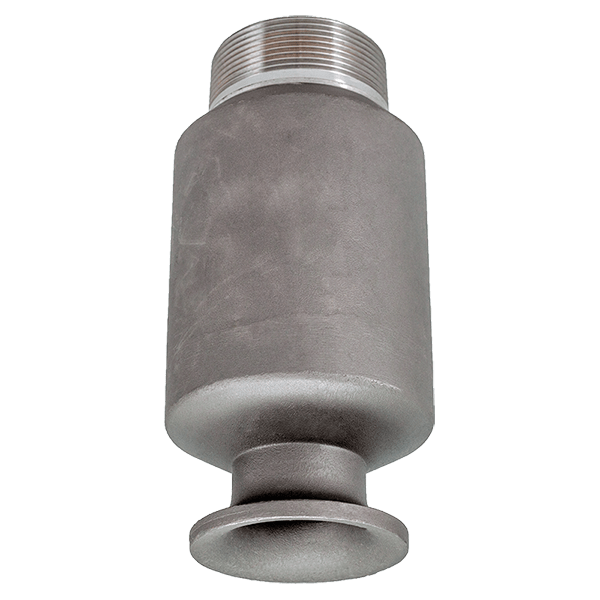
Common Uses & Industries
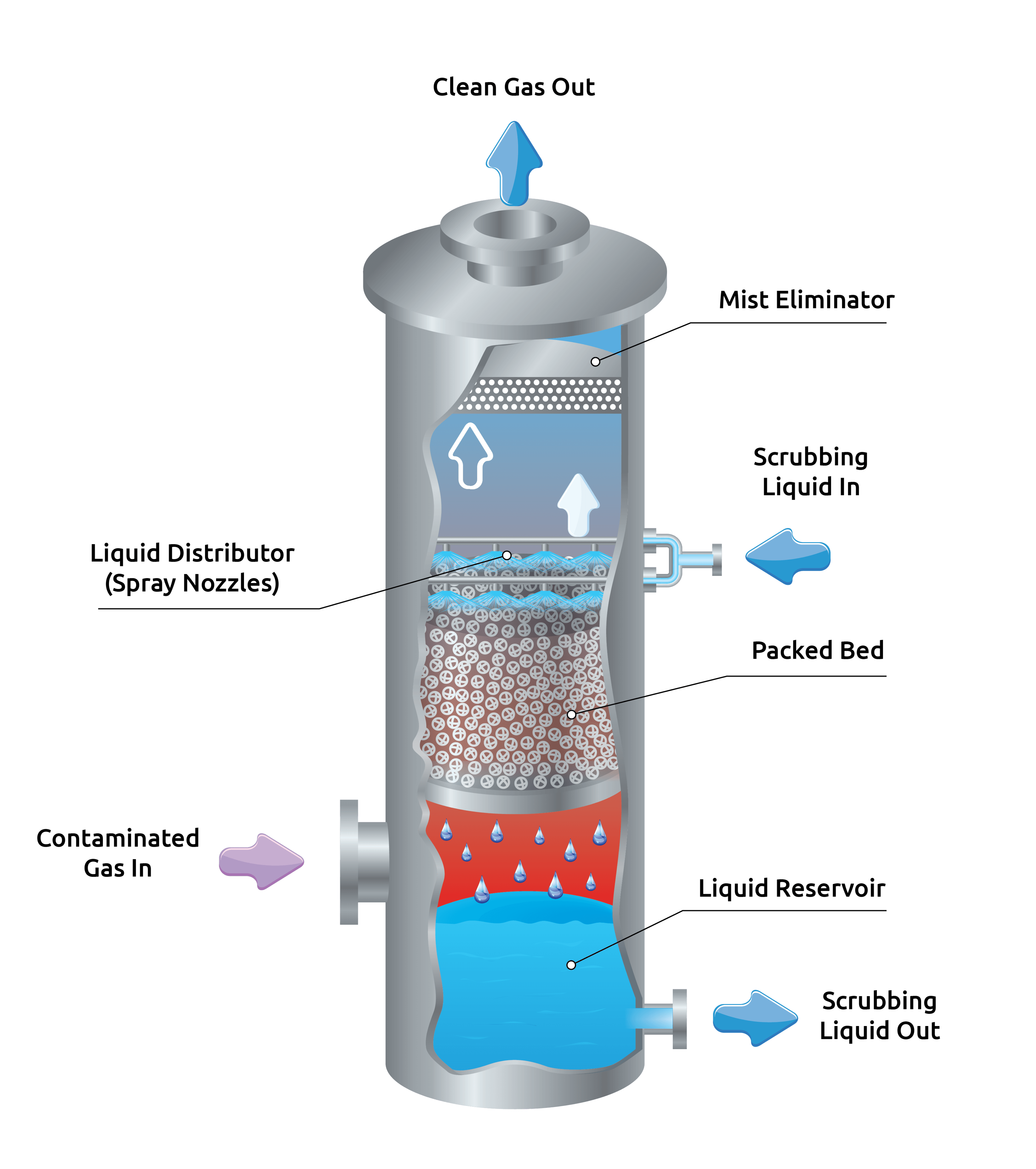
Important factors to consider:
Gas stream and contaminant to be scrubbed removed from the process stream
- Contaminant solubility/reaction speed with scrubbing fluid
- Temperature & particulate content
- May require a pre-quench or particulate removal process (i.e., venturi scrubber) upstream of the packed bed
Size and shape of packed bed scrubber
Process gas flow rates and velocities through the scrubber
- Allowable pressure drop
- Entrainment rates
- Avoid mist eliminator overload
Scrubbing fluid composition and solids content/filtration
Nozzle material of construction for corrosive environments
Available nozzle mounting positions and height above the packed bed surface
Available/required flow rate
- Gas/liquid ratio in the scrubber
Available pressure drop (∆P) across the nozzle
- ∆P = supply pressure at nozzle inlet – process pressure outside nozzle