Foam is a dispersion of gas (typically air) in a liquid. Air/gas can be entrained via agitation at the surface, such as a spinning impeller partially out of the liquid or a stream entering the free surface of a liquid (e.g., where a waterfall meets the pool at its base) or be created by biological or chemical reactions or processes.
Foam is undesirable because it can overflow vessels, create slippery and unsafe working conditions, interfere with processing, damage materials, and cause tanks to drain and dry slowly. Controlling foam can be accomplished by spraying liquid onto the pool, vessel, or reservoir’s surface, and allowing the spray’s droplets to impact the foam bubbles, causing them to break.
Common Uses & Industries
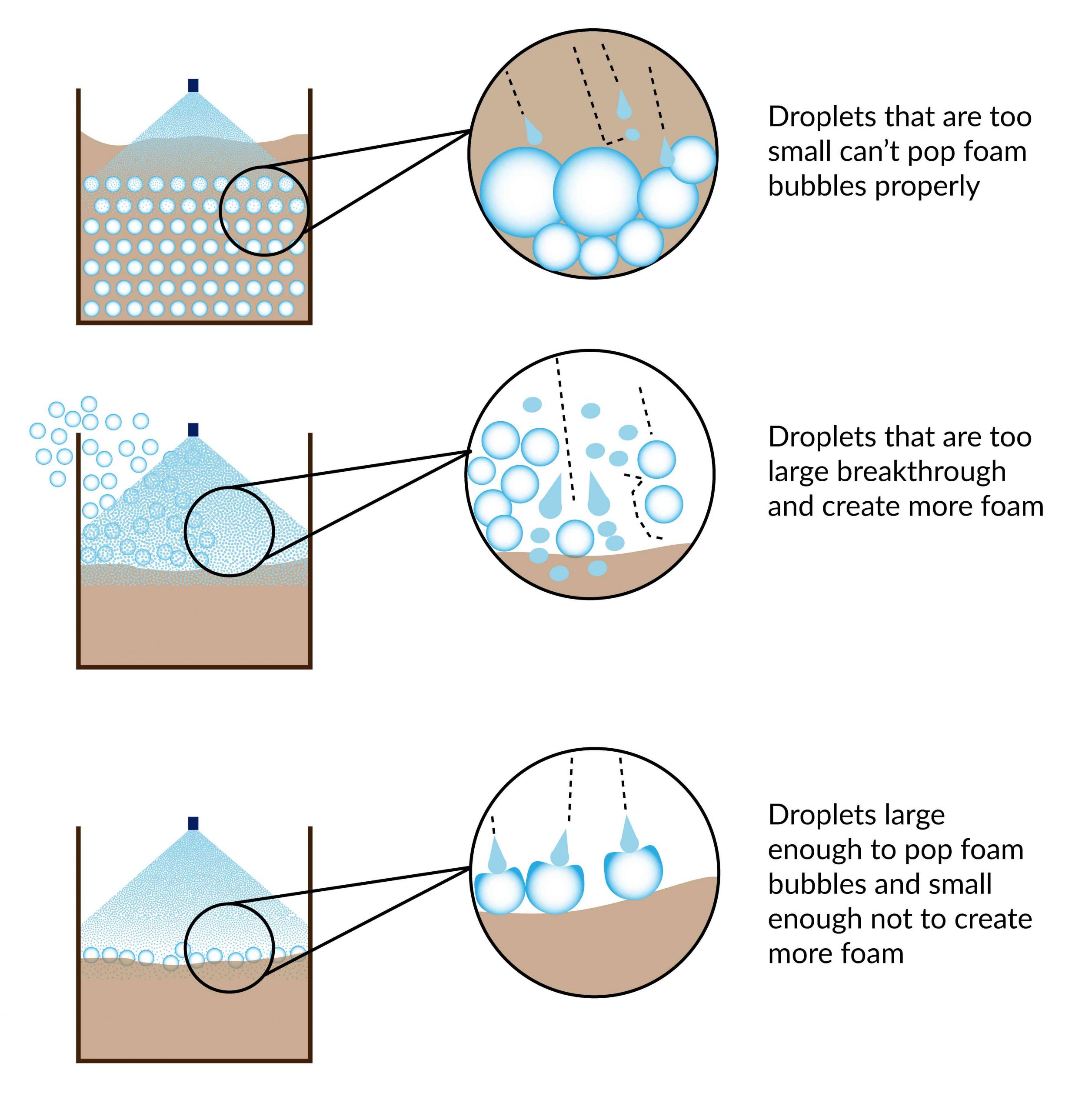
Important factors to consider:
Required coverage
- If the contents of a tank vessel are rotating, or the fluid is traveling in a trough or weir, a line of nozzles across the vessel can be used as the entire surface of the tank will pass under the line of nozzles after a complete rotation
Static vs. moving fluids
Available nozzle mounting locations
Foam thickness and rate of build-up (required drop size for break-up and mitigation)
- If the droplets are too small and have too little momentum, they will bounce off the bubble surface with no effect
- Similarly, if the droplets are too large and have too much momentum, they will crash through the bubble and impact the liquid below, causing more foam to be generated
Nozzle clog resistance
- As the foam control fluid is commonly recirculated, containing solids or waste particles, selection of the nozzle regarding clog resistance is important
Available pressure drop (∆P) across the nozzle
- ∆P = supply pressure at nozzle inlet – process pressure outside nozzle
- Typical operating pressures range from 5-20 PSI (0.3-1.4 bar) to produce a suitable droplet size and velocity for effective foam mitigation
Control high starch content in juice processing