It is necessary to keep tank contents mixed or agitated in many applications. Conventional mixing in a tank requires mechanical mixing components, such as a large, motor-driven impeller. However, many applications in which immiscible liquids need to be kept mixed or solids kept suspended may be done so with only a pump and submerged spray nozzles, greatly reducing system complexity, capital cost, and maintenance requirements.
Eductor mixing nozzles (BETE TurboMix) are completely submerged below the liquid in the tank and operate based on the simple premise that when velocity increases, pressure decreases. They are designed to take the velocity of the fluid pumped into the nozzle and convert it into a low-pressure zone that induces surrounding liquid in the tank to enter into the nozzle. In this fashion, the pumped fluid is effectively mixed with the tank contents, and the amount of fluid that exits the nozzle is three to five times the amount of fluid pumped. This multiplier effect allows greater mixing efficiency while using a smaller pumping capacity.
Even after liquids are combined, mixing nozzles can agitate the combined fluid. For instance, if the mixture has many lighter or heavier solids than the liquid, agitation prevents them from floating or settling. The same is true for liquids of two different densities or mixtures of oil and water-based compounds. Additionally, uniform liquids can stagnate, fostering bacteria growth and stratifying by temperature. Agitating keeps the solids suspended evenly while also preventing bacterial growth via mixing.
The most common setup consists of a pump-around system. The suction side of the pump is connected to the tank and draws off the liquid through this pipe. The discharge side of the pump is piped to the nozzle inlet. The liquid is drawn from the tank, through the pump, and into the nozzle. More liquid is entrained and emitted from the nozzle. The emitting stream propagates through the tank and keeps the liquid in the tank in motion. With the nozzles correctly located, agitating and mixing occur without moving components in the tank. Setups other than pump-around systems are also in widespread use. Fresh feed is supplied to the nozzle inlet rather than recycling it from the tank. Mixing of the fresh feed immediately occurs with the tank’s contents and then continues mixing as the exit jet propagates downstream.
Common Uses & Industries
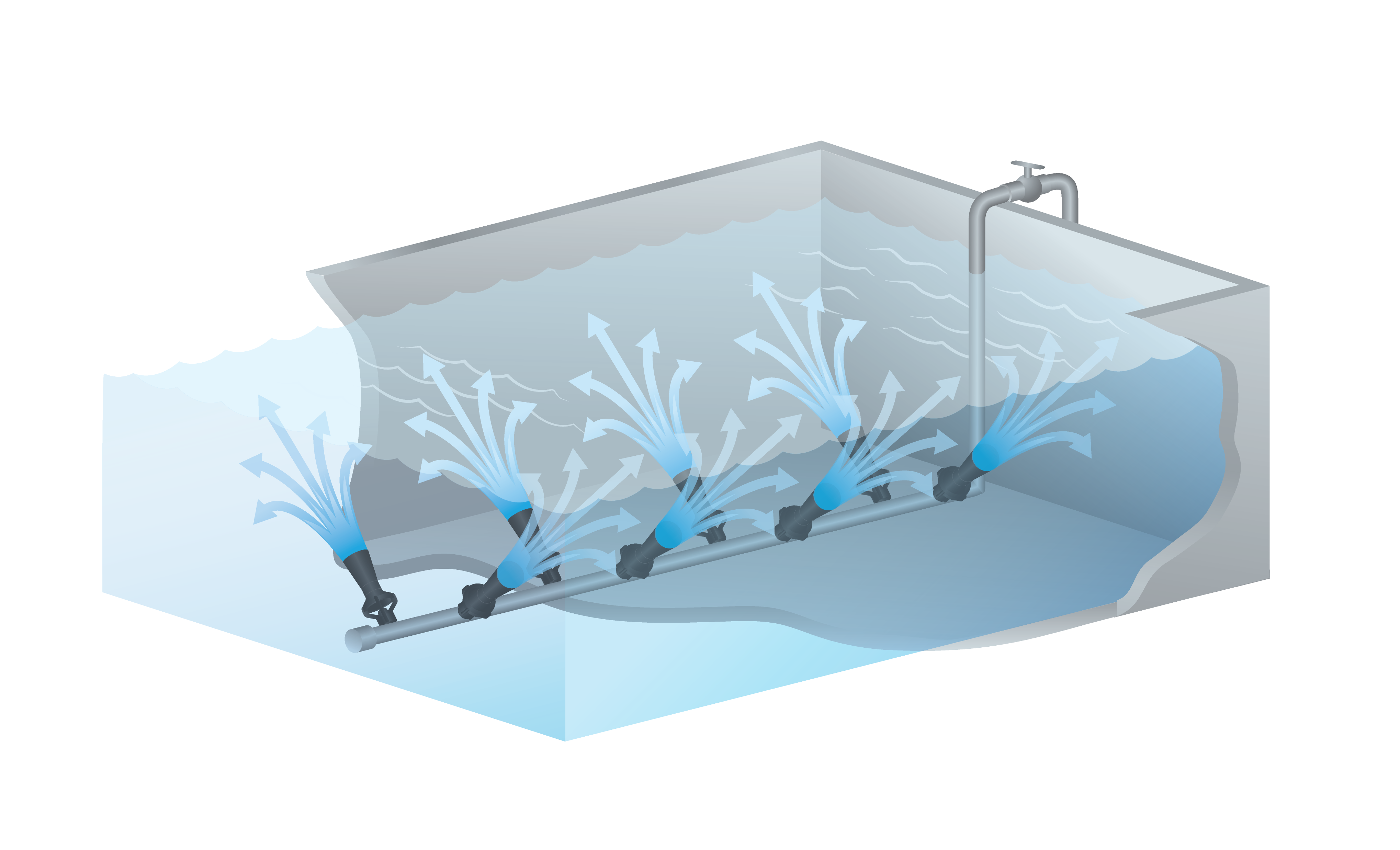
Important factors to consider:
Applicable design specifications and mixing requirements
- Circulation, agitation/solids suspension, mixing/blending, solids sweeping, etc.
Required material of construction for abrasive or corrosive environments
Size & shape of tank/vessel
Available nozzle mounting locations
Available/required flow rates
Available pressure drop (∆P) across the nozzle
- ∆P = supply pressure at nozzle inlet – process pressure outside nozzle