Computational Modeling & Simulated Spray Analysis
Spray testing in our lab is not always feasible. In these situations, our team of spray engineering experts uses a combination of computational fluid dynamics (CFD) and finite element analysis (FEA) to perform modeling simulations.
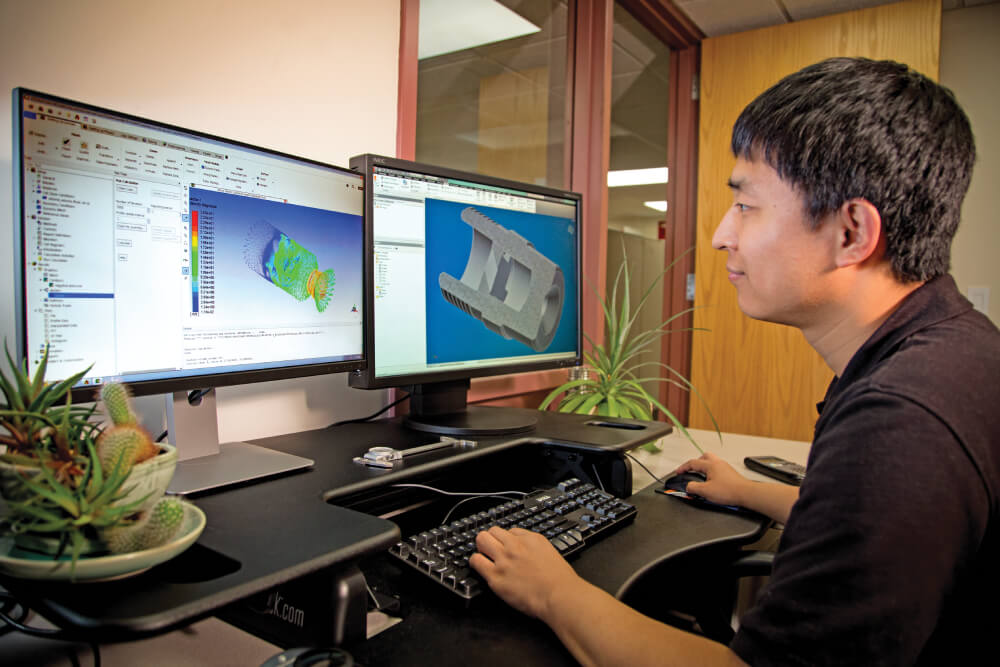
Computational Fluid Dynamics (CFD)
Computational modeling is an effective alternative when simulating an industrial process when physical testing is not feasible. Computational fluid dynamics (CFD) software, coupled with actual spray performance data captured in our laboratory, can model various systems to predict process performance.
CFD may be used together with physical modeling even when we can't reproduce the actual process in the lab. For example, if spraying a customer's material is impractical or hazardous, it may be possible to combine lab tests of a model using safe process fluids and conditions with a CFD model of the lab setup to validate a CFD model of the actual process.
CFD Simulations Include:
- Fluid flow inside nozzles and piping
- Evaporation of sprays and cooling of gases
- Spray trajectories
- Mixing in tanks
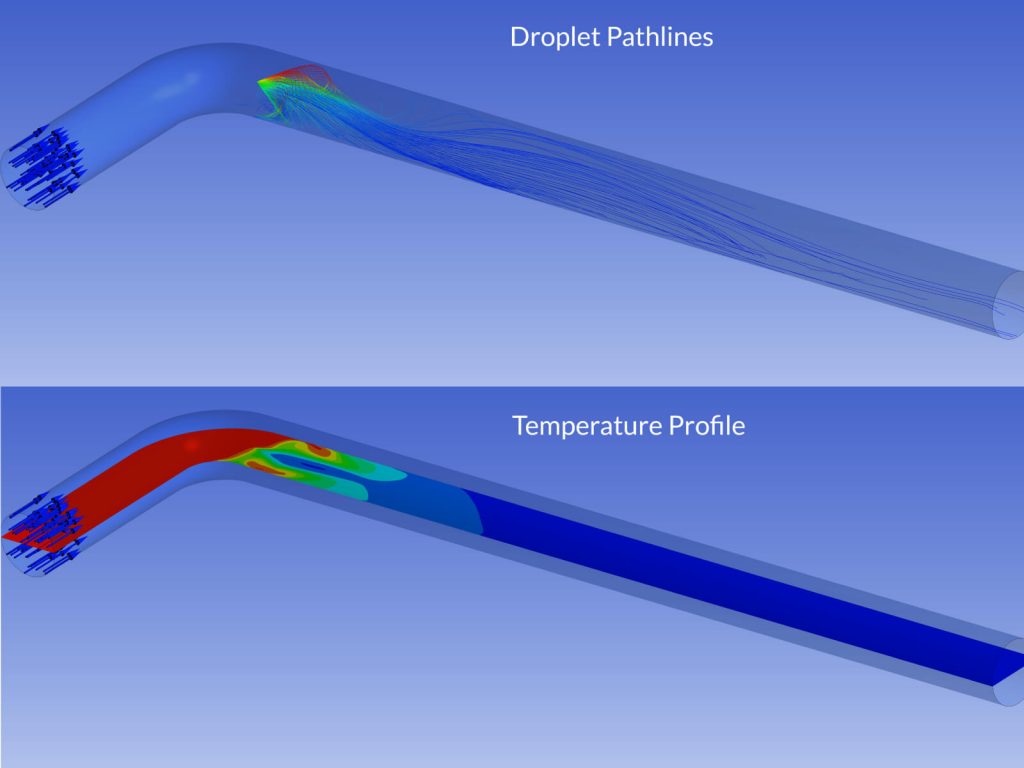
Finite Element Analysis (FEA)
BETE Uses ANSYS® Software for FEA Applications Including:
- Analysis of stresses in solid parts, especially for complex geometry or loading conditions for which analytical solutions do not exist
- Qualifying fabrications to ASME Boiler and Pressure Vessel Code Section VIII Division 2, part 5
- Computation of temperature distribution in solids and can be used together with CFD
- Calculation of mode shapes for vibration analysis and determination of eigenvalues to support buckling analysis
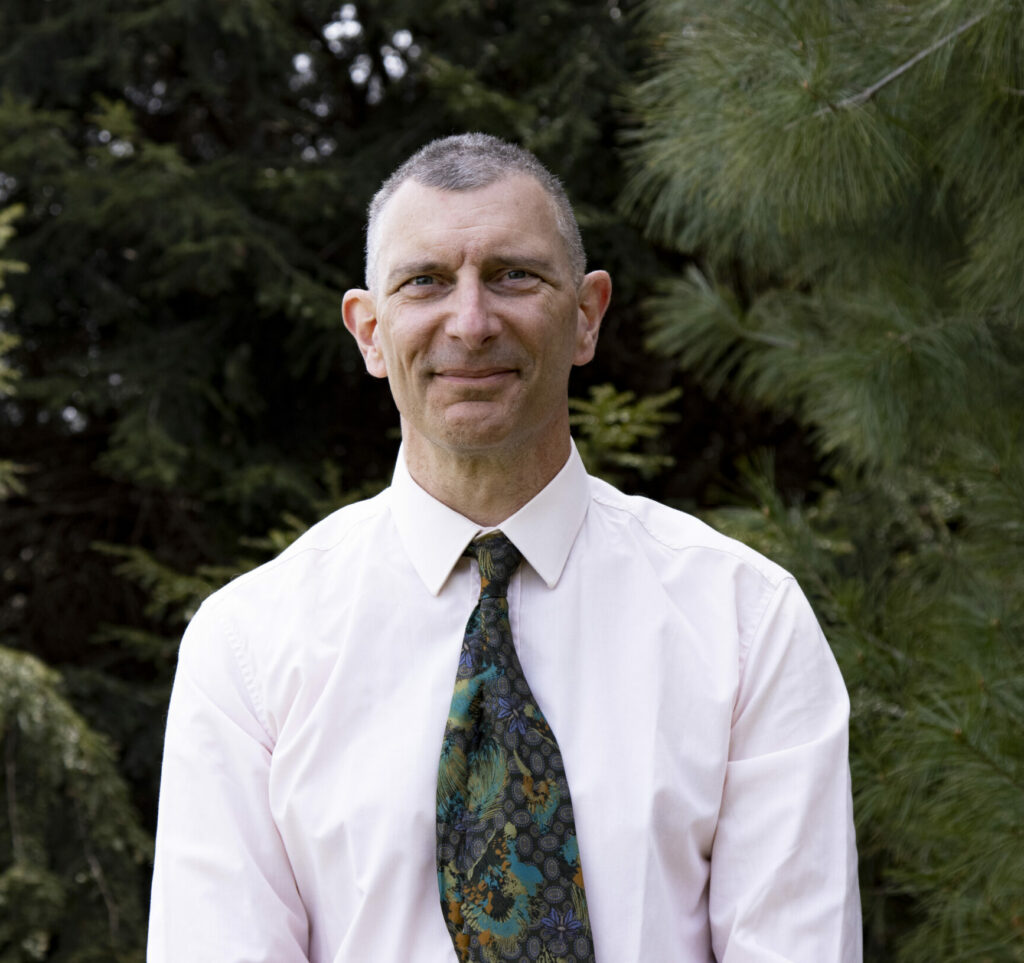