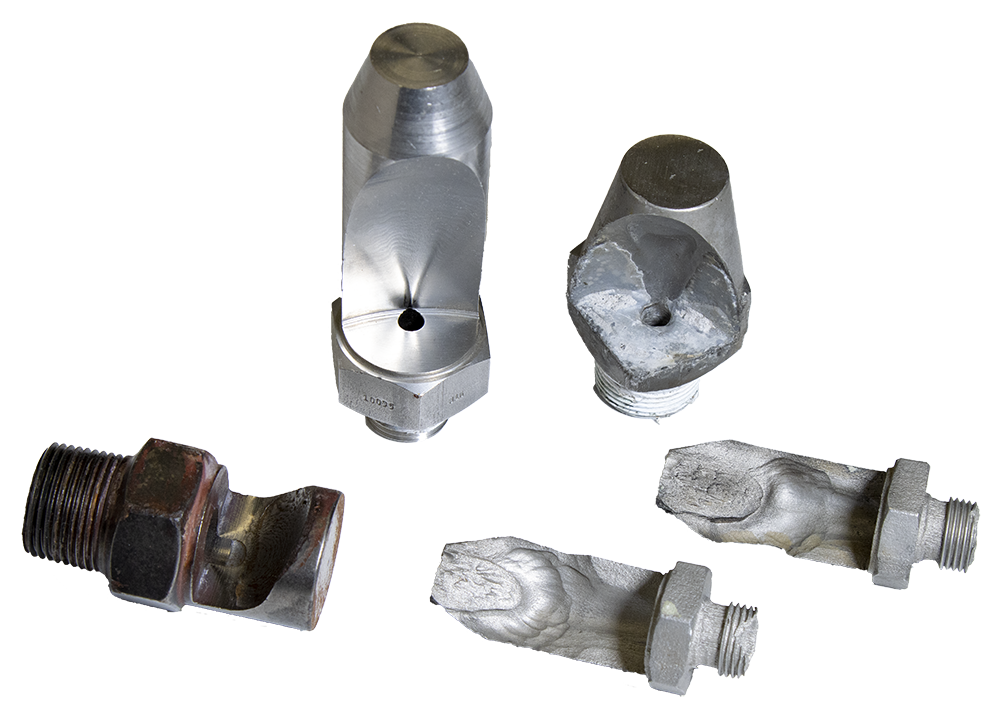
Why is Nozzle Maintenance Essential?
Spray nozzles are designed to deliver precise performance in terms of flow rate, spray pattern, and droplet size, ensuring the effective and efficient operation of an application or spray system. However, wear and tear on the nozzle’s internal structure and orifice can lead to various problems, such as distortion of the spray pattern, larger droplet sizes, and increased flow rates. These issues can negatively impact other equipment, overall process efficiency, and product quality. This article will teach us how to detect and prevent nozzle wear.
How Erosion and Corrosion Affect Nozzle Performance
The two main factors of nozzle wear that cause degradation of spray performance are nozzle erosion and corrosion.
- Erosion is the nozzle material and structure degradation caused by abrasive wear from the spray media or surrounding environment.
- Corrosion is the degradation of the nozzle material caused by a chemical attack and reactions between the nozzle material and spray media or environment.

In this example, a 10% increase in orifice diameter can result in more than a 20% increase in nozzle flow rate. In comparison, a 20% increase in orifice diameter can result in more than a 50% increase in nozzle flow rate and water consumption. This can lead to unintended consequences such as excessive resource usage or equipment malfunction.
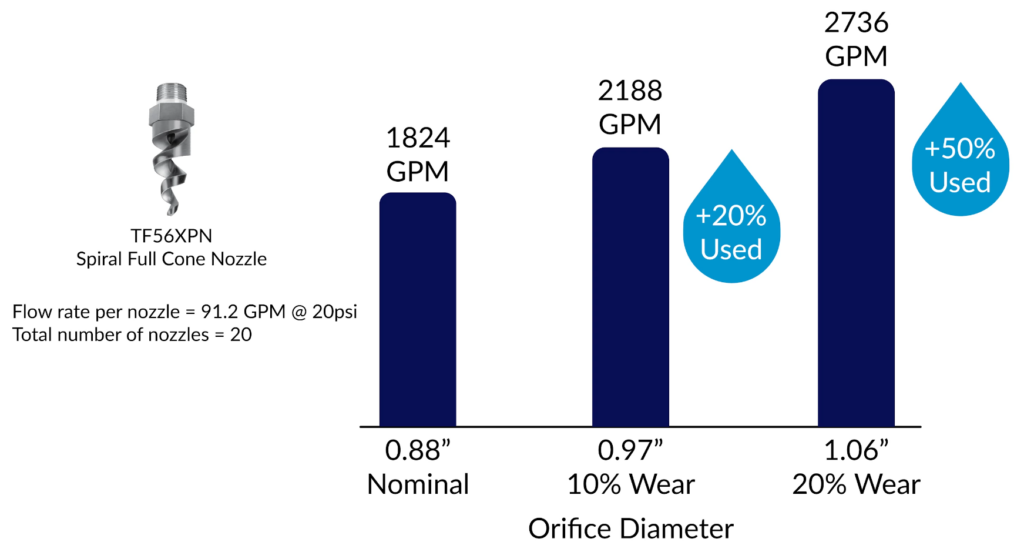
What Measures Can Be Used To Prevent Nozzle Wear?
Opting for suitable materials is the most effective approach to preventing excessive nozzle wear, but implementing additional preventive measures such as filtration can significantly prolong the nozzle’s lifespan. It’s crucial to monitor spray nozzle performance closely to notice and prevent potential issues from arising. There are several ways to do this.
- Visually inspect the nozzle for wear or damage.
- Visually observe the spray pattern for irregular streaks or uneven coverage.
- Monitor system performance and effectiveness by measuring flow rate and pressure and comparing them with target values such as outlet temperature and pollutant levels.
More Information on Optimizing Nozzle Performance With Monitoring & Maintenance
Implementing an effective nozzle maintenance program can pinpoint issues early, averting unplanned production halts that can lead to increased operational expenses and avoidable waste. BETE provides numerous maintenance tips for extending the nozzle lifespan, and our Applications Engineering department is available to address any further questions.