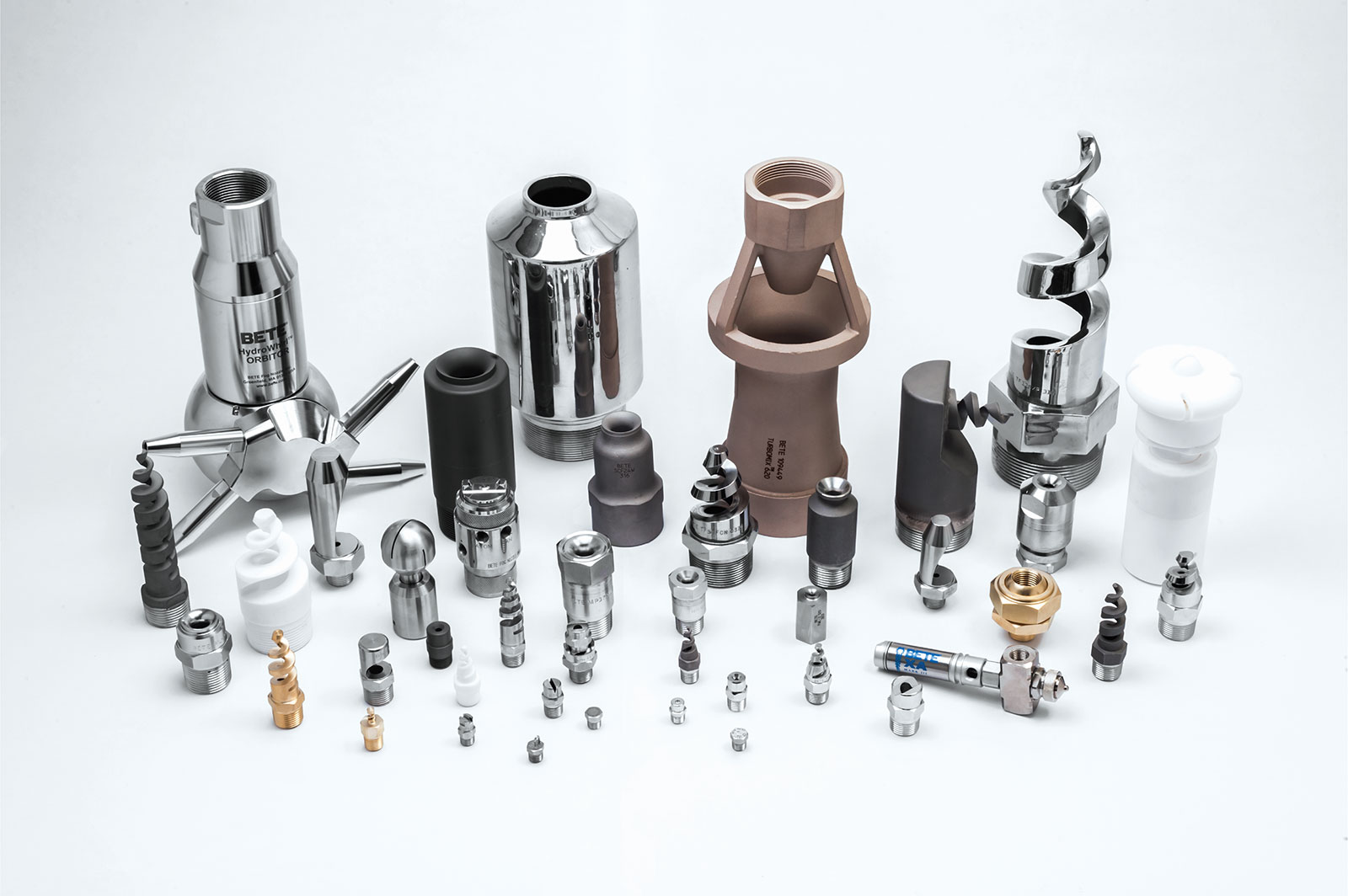
BETE has been engineering and producing spray nozzles for over 70 years. Over time technology and the number of applications for spray nozzles changed dramatically.
BETE has not only kept up with that change, but we’ve also set the pace with industry-leading technologies and products designed for industries all around the globe.
In this article, we’ll look at a few key categories of spray nozzles and why they are important in the nozzle selection process.
Spray Nozzle Considerations
BETE understands that no single spray nozzle can fit every application. That’s why we offer a dynamic range of nozzles and assemblies to fit many industries. There are a few factors to consider when selecting a nozzle.
Spray Pattern
A critical aspect of any nozzle is the spray pattern. BETE’s nozzle catalog features every spray pattern needed for industrial applications.
These include
- Fan
- Full Cone
- Hollow Cone
- Misting
- Air Atomizing
- Tank Cleaning
Each of these various spray types can be used for specific applications or used together to achieve the desired results.
Droplet Size
Droplet size can affect process performance and for some applications can be very critical. For humidification and cooling applications, small droplets are necessary because they offer more surface area to volume ratio, which reacts with the environment more efficiently. Larger droplets, however, are more effective for impact and cleaning.
Various types of nozzles are designed to produce different droplet sizes and this can help with your nozzle selection.
BETE uses an Imaging Particle Analyzer and a Phase-Doppler Particle Analyzer (PDPA) to measure droplet size.
Spray Angle And Spray Coverage
Spray angle and coverage are other critical characteristics of spray nozzles. BETE offers a full range of customizable options to fit many industrial applications.
Spray angle is typically measured from the nozzle orifice and is useful only for determining actual spray coverage close to the nozzle. As spray distance increases spray coverage can change because the spray width decreases depending on gravity and other environmental factors. This is typically referred to as actual spray coverage.
For most applications, actual spray coverage can be easily calculated but for more critical situations, theoretical testing may be needed to determine a more accurate spray coverage.
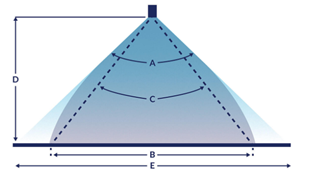
A – Spray Angle
B – Actual Spray Coverage
C- Effective Spray Angle
D – Spray Height
E – Theoretical Spray Coverage
Flow Rate
The flow rate for each nozzle depends on the application’s specific requirements. It is important to know that flow rates are calculated at the nozzle inlet.
The greatest influence on flow rate is pressure. Flow rate not only increases directly with an increase in pressure but does so at a consistent rate and the spray angle is affected.
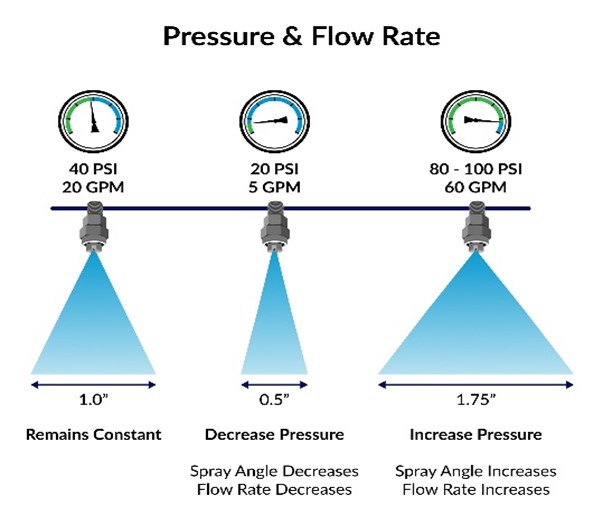
If the specific flow rate needed is not known, customers can contact a BETE representative for assistance to determine which nozzle is needed. Our engineers have worked in multiple industries and can help guide you through the process of nozzle selection.
Spray Nozzle Materials
BETE offers spray nozzles in various materials to fit industry-specific applications. Specific alloys are needed for chemical and petrochemical industrial applications to deal with corrosive or abrasive environments. BETE offers spray nozzles in various materials to fit industry-specific applications.
We also offer hygienic materials for food and beverage applications and other industries where material selection is regulated to meet safety standards.
Spray Assemblies and Spray Systems
Beyond spray nozzles, BETE offers engineered spray assemblies and complete spray systems customized for your application or industrial process. Our systems can be completely stand-alone or integrated into your existing plant.
Complete Information On BETE Spray Nozzles
Whether you’re simply choosing a nozzle or designing a complete spray system, BETE has a solution for you.
Contact BETE today to speak with our expert product consultants to learn which nozzle or system can best improve and modernize your current operations.