Overview
INCONSISTENT APPLICATION OF SEEDS
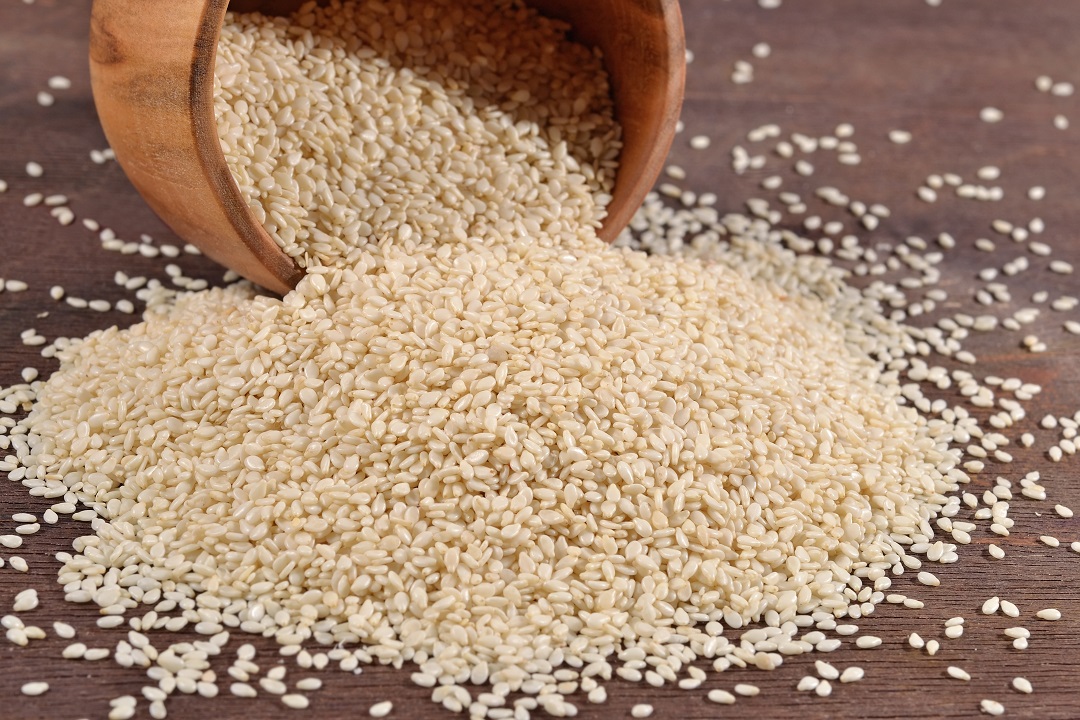
THE BETE FLEXFLOW® WITH ELECTRIC HYDROPULSE® AUTOMATIC SPRAY NOZZLES
BETE engineers visited the manufacturer to demonstrate the FlexFlow Precision Spray Control System. Impressed by the range of cycle frequencies, duty cycles, and pressures varying up to 40 PSI, the cracker manufacturer was also interested in the FlexFlow’s multiple operational zones. At times, the assembly line would hold crackers up to five rows wide — at others, nine. The FlexFlow would be able to spray at both ranges, keeping the application consistent and reliable.
Advantages of the FlexFlow System with HydroPulse Nozzles include:
- Precision spray directly on the target
- Reduced waste and minimal overspray maintains a clean, safe environment
- Uniform and repeatable coverage improves product quality
- Interchangeable nozzle tips provide a wide range of spray patterns to match process requirements
- Flow control with Pulse Width Modulation (PWM) ensures constant pressure and spray performance
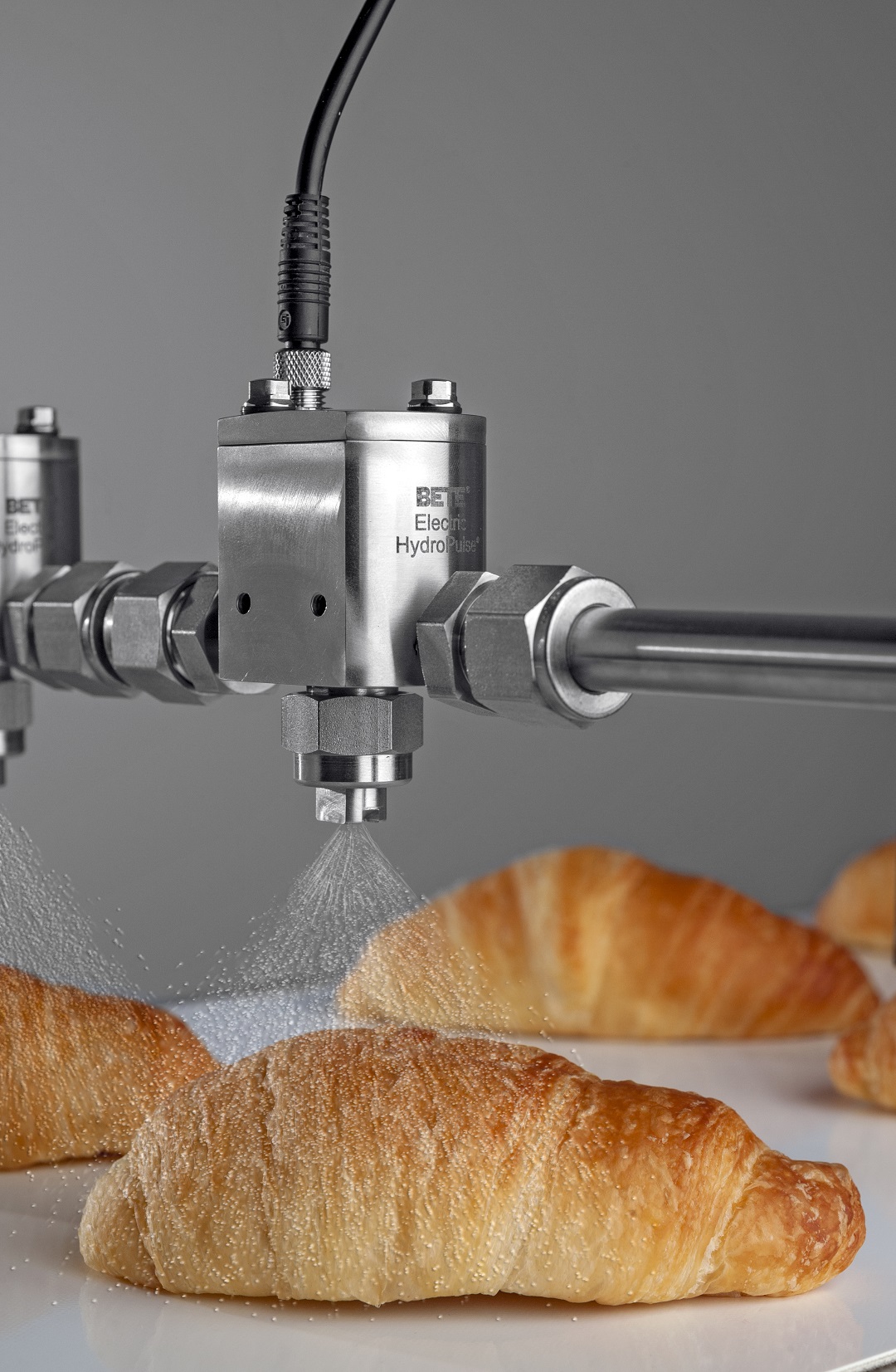
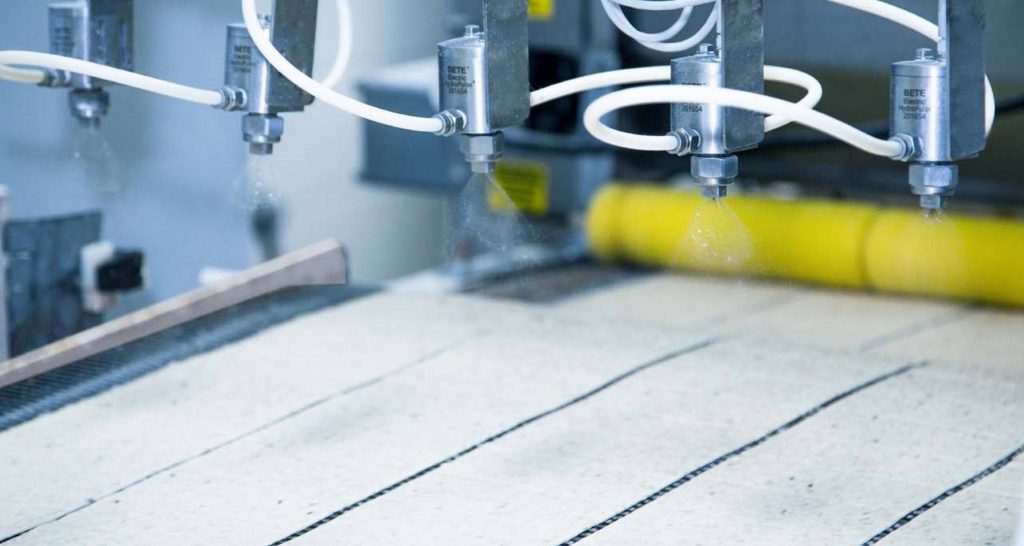
RESULTS
The customer’s process now features consistent, uniform spray coverage onto the crackers. Seeds stick firmly, and there is a significant reduction in overspray, wasted ingredients, and downtime — resulting in the following cost savings:
- 15% savings in sesame seeds
- Increased production time with improved quality of the crackers
- A massive reduction of 12 hours per month downtime compared with the previous year
- Daily cleaning now takes half as long — only one hour compared to two